未来テクノロジー
テクノロジーが拓く、豊かな未来。挑戦し続ける人と企業をクローズアップ
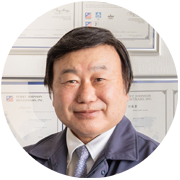
中島 秀敏さん
株式会社ピュアロンジャパン 代表取締役CEO
北海道池田町出身。中学生のとき、日本最北の国産ワインのためのブドウ畑作りを手伝ったことが、ものづくりの原点。関西大学法学部を卒業し、化学系商社へ就職。塗料や劇毒物などの取り扱い、機械販売・メンテナンスを行う。その後、製薬会社の研究職に転職。1985年、半導体回路製造に必要なフィルターなどを作る株式会社ピュアロンジャパンを創業。趣味は陶芸、絵画鑑賞。
半導体製造装置向けの高精度フィルターに関して、世界トップクラスの技術力を持つ株式会社ピュアロンジャパン。10年以上の歳月をかけ開発を続けてきた医療用冷陰極X線撮影機器は、地域復興実用化開発等促進事業費補助金(以下、実用化補助金)を活用することで量産化の目途がたった。さらに、日本だけでなく海外マーケットへの販売も視野に入れている。代表取締役CEOである中島秀敏さんを訪ね、長年にわたる研究開発への思い、今後の展望などをうかがった。
タブーに挑戦し、世界一のガスフィルターを製造
流体制御メーカーとして、オンリーワンを目指す
ピュアロンジャパン創業のきっかけは、中島さんが製薬会社で製品開発に携わっていた1980年代まで遡る。薬の有効成分を調べるためには、細菌を補足するフィルターが重要だが、ある大企業が開発したフィルターが公表通りの精度になっておらず、細菌が全く取れない事実を知る。
なにかよいフィルターはないかと悩んだ中島さんが思い出したのは、数年前、京セラの技術者から聞いたセラミックだった。調べてみると電気特性が非常によく、有用性が高いことが分かった。当時は水用フィルターが一般的だったが、中島さんはあえて半導体製造に使うガス(をろ過する)フィルターを開発することを決める。しかも、半導体の世界ではタブーとされていた、ガスフィルターの素材にセラミックを使う手法を選んだ。
「半導体製造にはさまざまなガスが使われ、1マイクロメートル(1000分の1ミリ)単位のゴミを除去する精度が求められます。非常にレベルの高い半導体業界で、まだ誰もしたことのないフィルターを完成させれば、どの業界でも成功できると思ったんです」
いわき市内郷にある環境・開発 中央研究所(エコラボ)。社名の「ピュアロン」は、「pure(純粋、真)」と「electron(電子)」からなる造語。フィルターによって清浄(pure)なガスを作りだし、圧力センサなどを用いた流体制御において、ごまかしのきかない真正な(pure)な製品作りを目指す。electronはX線に欠かせない電子
ピュアロンジャパンを創業し、セラミックガスフィルターが完成。当時、会社近くにあった半導体メーカーでは毎日のようにフィルターを交換していたが、同社が開発したセラミックガスフィルターは、2週間たっても破損や目詰まりがなかった。この製品は半導体業界にとって一つのブレイクスルーとして迎えられ、半導体素子メーカーのインテル社をはじめ、多くの工場で次々と採用されることになった。その後、世界特許を取得。開発から35年がたった現在でも、世界最高精度を維持している。
さらに、同社の技術力を象徴する製品に「絶対圧センサ」がある。従来のダイアフラム式圧力センサは熱の影響を受けやすく、人が軽く握っただけでも数%の誤差が生じていた。そこで同社は、センサの中に(例えば)1気圧を閉じ込め、高度1,000mでも、海抜マイナス100mでも、周りの環境がどんなに変化してもセンサ内の気圧が変わらない高精度センサを日本で初めて開発。高圧ガスの制御、ICチップ製造の歩留まりを大きく改善し、業界の標準機として広く使われることになった。
画期的な冷陰極X線管が
在宅医療や救急医療を変える
レントゲンなどに使われる一般的なX線管は、電子源に熱陰極(フィラメント)を使いX線を放出している。そのため、温度を維持するために高電圧システムが必要不可欠で、据え置き型といった大きな装置になってしまう。さらに、安定して使えるまで15分程度の予備加熱も必要だった。この問題を解決するのが、同社が10年以上前から開発を続けている医療用冷陰極X線管だ。
「独自開発したプラズマCVD(化学蒸着)成膜方法という特許取得済みの技術を使い、カーボンナノチューブ製の冷陰極電子源を作ります。電子源を拡大すると、カーボン炭素が高密度に分布し、まるで草原のような滑らかさなんですよ」と中島さんが説明してくれる。
冷陰極X線管の特徴は、消費電力を抑えられ、小型化できること。消費電力が小さいため、モバイルバッテリーや単3乾電池で駆動し、停電の心配がない。また予備熱が不要ですぐに使えるため、緊急時の処置が必要な事故現場などでも活躍してくれる。
「小型化のメリットは大きく、簡単に持ち運べ、その場で撮影し患部や病状を診たり、早期発見、早期治療に役立てられたりします。検診の他にも在宅医療や介護施設、さらに過疎地や離島でのX線撮影や診断が可能になります。撮影した画像も鮮明なので、離れた病院にいる医師にデータを送信し、指示を仰ぐといったことも現実味を帯びてきます」
ついに完成した冷陰極X線管。電線などのインフラ検査装置、空港や新幹線などでの手荷物検査など、小型化の実現によって活用範囲が広がる
装置の核となるカーボンナノチューブは、次世代の半導体素材として期待されていたこともあり、同社で長年研究を重ねてきた知見が今回の開発に生かされた。X線管は、ろう付けという技術で冶金(やきん)接合技術を使いセラミックと銅を接合している。陶磁器であるセラミックと金属を接合することは非常に高い技術力が求められ、真空での作業ということも開発を難しいものにした。そこで実用化補助金を使い、超高真空ろう付け炉を購入。開発は一気に進み、量産化の道筋も見えた。
開発者として人の役に立つものを残したい
小さな成功の積み重ねが、大きな成功を生む
X線管の開発を10年以上も続けられたモチベーションはどこにあるのだろうか
「実は社内でも、特に経理から開発をやめてくださいと言われていました(笑)。それでも、誰もなし得ていないことを形にしたかったですし、誰かの役に立つもの、この世に残せるものを作りたかった。難しいからこそチャレンジする意味がある。だから、世界一であり、オンリーワンでなければならないんです」と、ものづくりへの思いを語る。
社会的意義の大きな製品でありながら、開発メンバーは3〜4名ほどと少数精鋭。半導体メーカーからの転職者もいたが、X線とは全く関係ない事業部からベテラン技術者が集められた。開発が難航しても、こうしたら面白いかもと、専門外だから思いつくアイデアを採用し、試作を重ねた。「新しいものを生み出すには、ひらめきと興味本位が大切だ」と中島さんは言う。
開発メンバーと一緒に。写真左から、X線作業主任者の中山幸久さん。中島社長。メディカル事業部マネージャーの田口廣治さん
「最初は無理だと思っていたけれど、小さな成功を積み重ねるうちに、もしかしたら作れるかもと思うようになっていった。今では目標と道筋が見えています」と話すのは、開発メンバーの1人、メディカル事業部のマネージャー田口廣治さん。
「失敗するかもしれないけれど、チャレンジできたのは実用化補助金のおかげです。うちのような中小企業が200万、300万の機材を簡単に買えませんから。補助金がなければ、X線管は完成していなかったと思います」
冷陰極X線管の実用化開発はほぼ完了し、量産準備に入っている。福島県内の医療機関の協力もあり、医療用X線管試作機の実証テストやデータ取得が行われ、実際の医療の現場の評価やニーズを反映しながら、より高い完成度に仕上げていく。
利用者の声を製品開発に生かす
日本だけでなく、アジア市場にも進出
現在取り組んでいる冷陰極X線管を使ったCT(コンピュータ断層撮影)の小型化も、周りからは無理だと言われているそう。
「車に例えると、冷陰極X線管はエンジンのスパークプラグに過ぎないんです。なのに、車(小型CT)を作るぞって言っている。周りが無理だと言いたくなる気持ちも分かります(笑)。完成すれば世紀の大発明ですが、一筋縄ではいかないから世の中にないんです。でも、小さな成功を重ねるとできることが分ってくるんですよね」と笑う田口さん。
地域経済の中心的な担い手として、成長性が期待される企業に送られる経済産業省「地域未来牽引企業」に認定された
開発メンバーで、営業担当でもある中山幸久さんは、製品化のヒントは現場にあると言う。
「今までのCTは大きく、患者さんが横になる必要がありました。例えば、膝や腰が痛い患者さんも寝ると痛みが治まってしまい、うまく診察できないこともありました。でも、持ち運びできる小型CTなら、痛い姿勢のまま検査できるので、より正しい治療ができます」。他にも、訪問診療や災害現場での診療などを想定し、数年以内の販売を目指している。
「作りたいものはあるけれど、どういうものを作ればいいか分からないし、どうやって作ったらいいかさえ分からない。でも、お医者さん、患者さんの負担を減らしたいという目的地があるから、なんとか前へ歩いて行けるんです」(田口さん)
半年ほど前、50代ばかりだった開発メンバーに27歳の石原啄磨さんが加わった。
「以前は精密機器メーカーで製造開発の仕事をしていましたが、メディカルの仕事をしたく転職しました。今は、超高真空ろう付け炉を担当しています。経験の浅い僕の意見でもちゃんと話を聞いてくれ、アイデアとして採用してくれるのがうれしいですね。」と話す姿から仕事へのやりがいを感じられる。
「X線管などの開発や製造は、品質維持の観点からも浜通りで行う予定です。今後は、タイの医療機器メーカーと連携し、東南アジアや日本マーケットでの展開を目指しています」と話す中島さんは歩みを止めない。
困難に直面しても決して諦めないまっすぐな気持ちが、夢を叶える原動力に違いない。
株式会社ピュアロンジャパン
1985年創業。タブー視されていた開発に挑戦し、世界初の半導体製造ライン用セラミックガスフィルターを完成させる。標準コンダクタンスエレメント(SCE)は、大学の研究機関や宇宙航空研究開発機構(JAXA)などに採用され、質量分析器の校正では国際基準を得ている。また、2014年には医療機器製造業許可書を取得し、翌年には医療機器の品質マネジメントシステム「ISO13485:2003」を取得。流体制御機器、医療機器、工作機械、精密機器など、幅広い分野の製品開発を手がける。